By Pete Frentzos, Radco Industries Inc.
Defining “food grade” and a new set of regulations from NSF International make it easier for process engineers in food manufacturing to choose a heat transfer fluid.
Until recently, the term “food grade” has been used loosely to describe heat transfer fluids that are suitable for food processing applications. It has not been a term that specifically describes heat transfer fluids in their stated use but was an inference made from other regulations. There was an enthusiastic salesperson who would take a drink of fluid to prove to his customers eth validity of this inference. While possibly valid, it’s not recommended.The Food and Drug Administration (FDA), Washington, under a wide range of regulations, defines the food additive status of a number of products, but not specifically heat transfer fluid. One can refer to Title 21 of the Code of Federal Regulations (CFR) online (see sidebar “See for Yourself”). These chemicals are listed under part 170 subsections. It covers additives designed for indirect food additives, secondary food additives, indirect food additives of a specific chemical family, and so on. Because the same chemicals can be part of a heat transfer fluid product line, this became one of the standards called “food grade.”
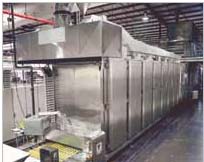
Founded in 1944 as the National Sanitation Foundation, NSF International, Ann Arbor, Mich., is known for the development of standards, product testing and certification services in the areas of public health, safety and protection of the environment. NSF became involved when the USDA decided that it would no longer maintain its list. At first, NSF acted as record keeper to ensure the list was available for review. Now, the organization has taken an active role to refine the list. NSF created the Non-Foods Compound Group to define the use of heat transfer fluid, fluid additives and lubricants, as well as other materials, separately for their specific applications.Likewise, until recently, the United States Department of Agriculture (USDA), Washington, had its own regulations, which included mineral oils used as machinery lubricants and release agents to prevent meat from sticking to grills. The reference, H1 status, was used to indicate that the oil was acceptable for use in meat and poultry establishments and could have incidental food or feed contact. Again, these same mineral oils can be part or all of what is used as a “hot oil” for heat transfer.
Kenji Yano, program manager of the nonfood compounds registration program explains, “The term ‘food-grade’ is not used. …Instead ‘incidental contact’ (HT1) is used as opposed to ‘nonfood contact’ (HT2) compounds.” NSF keeps this list online, on CD and in its “White Book,” which is published annually.
Qualifying Fluids and Specific Uses
When to use which type of heat transfer fluid depends on the requirements of the application.
Whether you choose FDA or NSF as your current guide, there are many fluids from which to choose. As an example, within the following chemistries are select fluids that are safe for “incidental food contact” — brine, potassium formate (KF), polyalphaolephin (PAO) and highly refined, severely hydrogenated paraffinic white oils. Both PAO and white oil chemistries are heat transfer fluids sometimes referred to as “hot oils.” When to use which one depends on the requirements of the application; each has its own advantages and temperature ratings (table 1).
When HT1 must be specified is easy to understand. If there is any chance of incidental food contact, it should be a requirement, even if not regulated, as a matter of good manufacturing practice. It is good economics, too. For example, a packaging line heats adhesive with heat transfer fluid. The adhesive is used to seal frozen food packaging. If a leak occurs in the heat exchanger, it could go undetected for a long time, and any premium paid for “incidental food contact (HT1)” fluid wouldn’t seem like much compared to a hundred thousand units of contaminated packages. There also is the matter of storage and overall production standards. The heat transfer fluid used should complement the environment where it is required.
When the temperature requirement of the application exceeds 600oF (316oC) or surface temperatures on the heat exchange surface exceeds 650oF (343oC), the type of heat transfer fluid rated for incidental food contact should not be specified. At this point, the white oils, the highest temperature rated product of the group, do not have the thermal stability required for a long life. (There is some debate on this exact temperature, but 600oF bulk operating temperature is a good conservative number to work with.) In this case, aromatic/synthetic fluids or other high temperature fluids are the only choice.
Beyond Food Use
Not every application needs to be in food processing to use HT1 fluids. A good example is the die-cast industry. The molds are heated, cooled or held at steady temperatures using heat transfer fluid. When the molds are opened or changed, some heat transfer fluid typically leaks from the inner chamber. The leaking fluid is captured for disposal, but this involves employee exposure to the fluid. HT1 fluids made from white oils are easy to handle because they are nontoxic and nonirritating to the skin. The lack of odor also results in fewer employee complaints.
Due to the efforts by NSF International, process engineers, specifying engineers, maintenance engineers and technicians now can take advantage of a simple and straightforward guide for the type of fluid they want. There is no need to rely on a sales pitch or to sort through the voluminous FDA regulations and guess if a fluid really qualifies.
Sidebar: Heat Transfer Fluids and Kosher Foods
Another specifying consideration in food processing is the need for kosher heat transfer fluid in applications that manufacture kosher products or products to be used in kosher foods. Even though heat transfer fluid is not put into the food directly, it must be kosher under the kosher laws that refer to heating a product through a common wall (in this case, a heat exchanger).
Rabbi Sholem Fishbane of the Chicago Rabbinical Council (CRC), a kosher overseer agency, explains that this is an important requirement. Kosher laws state that this type of heating causes a mixture of flavors. Under kosher law the “spiritual flavor” will go through the metal and affect the liquid on the other side. If the kosher product is heated by a fluid that is not kosher, explains Rabbi Fishbane, this spiritual flavor will contaminate the kosher product.
The concept of the mixing of flavors can lead to some interesting engineering issues. If a plant is broiling kosher chickens with a heat transfer fluid system and using the same fluid to process animal fats that contain pork in another part of the plant, under kosher law, the process has been contaminated. Likewise, in plants that produce both kosher and non-kosher or even dairy and pareve (non-dairy), engineers must carefully review details like returned condensate.
The CRC makes frequent random inspections and is diligent in educating themselves to understand plant engineering, ensuring that kosher laws are not broken. This is of great service to the food processor by giving assistance to their process planning and provides a third-party certification of product quality. Rabbi Fishbane emphasizes that this requires a technical education supported through “constant attendance of seminars and lectures” and “not every agency’s approval is acknowledged by the CRC.” A specifying engineer needs to determine which agencies have the ability to make the types of inspections required for the specific application. Each heat transfer fluid manufacturer has the information on which agency they use.
A note on kosher fluids is that the fluid also should be rated as kosher/pareve, which means it can be used for foods and additives intended for consumption on Passover and used all year.
When the temperature requirement of the application exceeds 600oF (316oC) or surface temperatures on the heat exchange surface exceeds 650oF (343oC), a heat transfer fluid rated for incidental food contact should not be specified. What about kosher? Kosher law allows for a non-kosher fluid heating medium if that medium is made so foul that any contamination would make the food or additive that is heated inedible. By their nature, aromatic chemistries used for higher temperatures have a strong, pungent odor, especially when heated, and qualify readily for this exemption.
Sidebar: See for Yourself
Visit these web sites for more information.
Pete Frentzos is product manager at Radco Industries, La Fox, Ill.